Yardımcı Pilotunuzu Alın
Create Chatbot For Manufacturing
Revolutionize your manufacturing processes with state-of-the-art AI-powered chatbots. Elevate productivity and efficiency with Streebo's innovative solutions designed for the manufacturing sector.
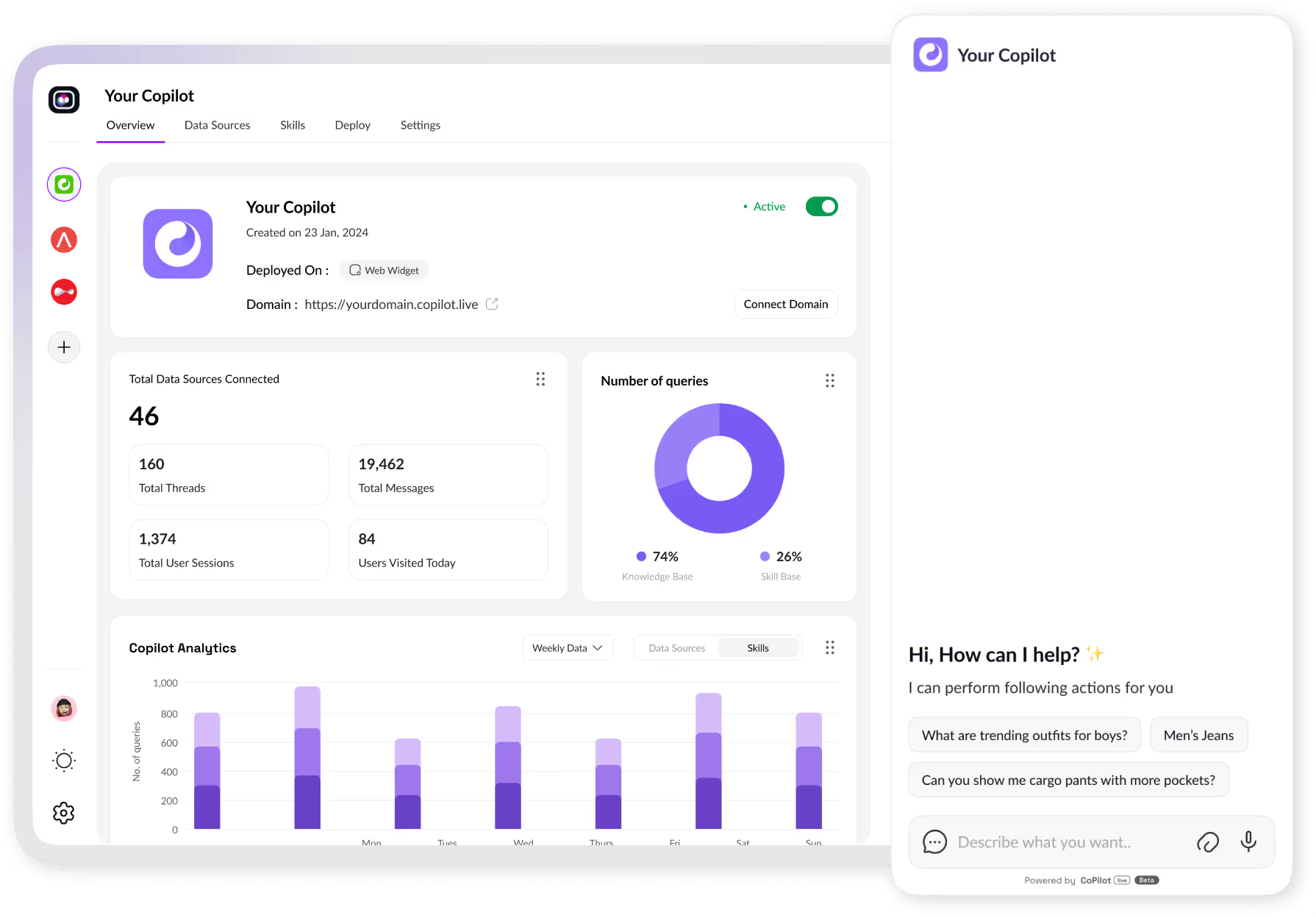
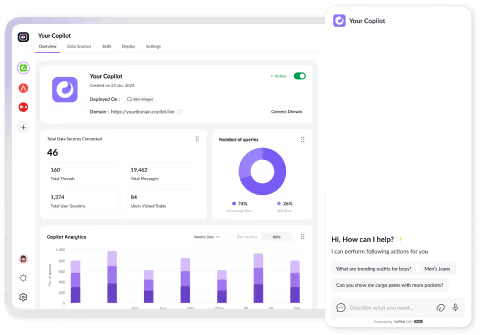
Create Chatbot For Manufacturing
Revolutionize your manufacturing processes with state-of-the-art AI-powered chatbots. Elevate productivity and efficiency with Streebo's innovative solutions designed for the manufacturing sector.
Yardımcı Pilotunuzu Kurun
It Takes Just a Minute
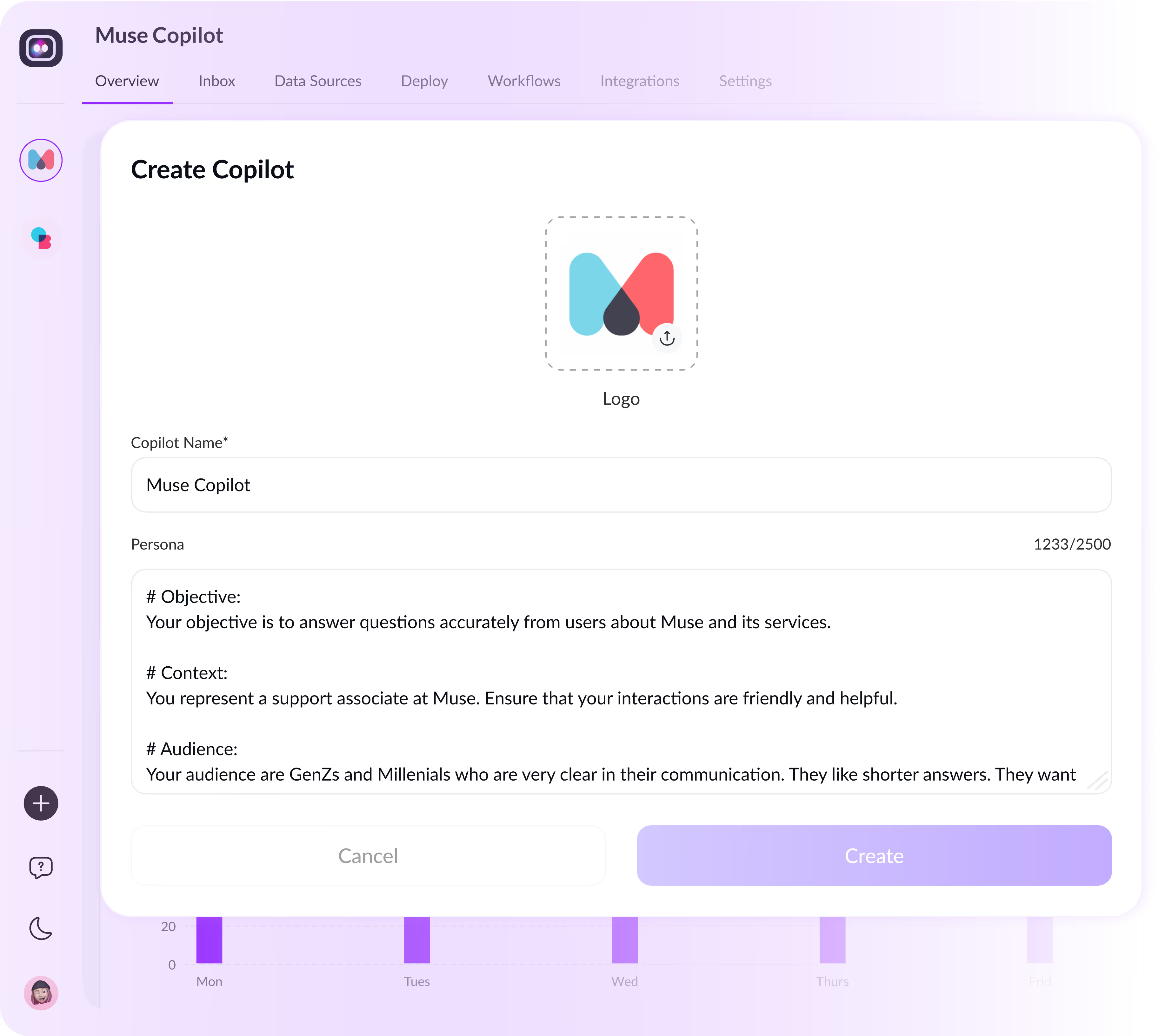
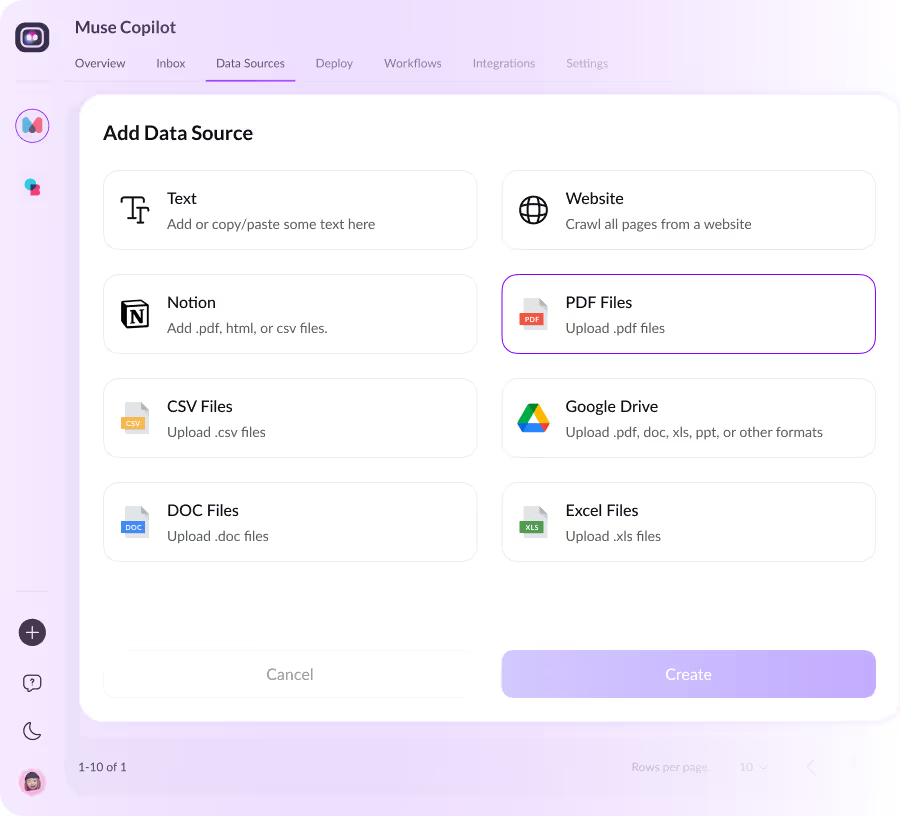
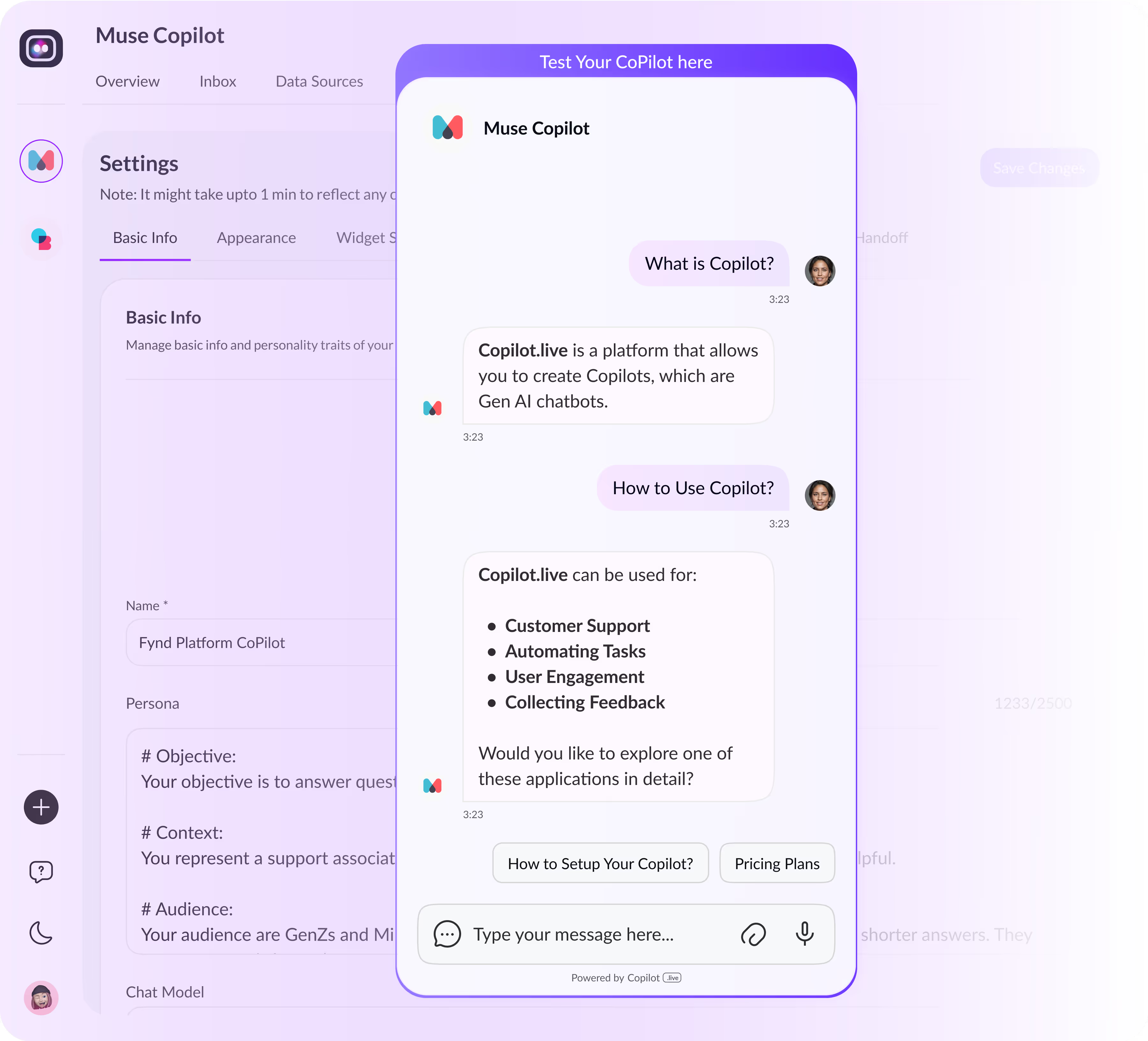
Craft Your Manufacturing Chatbot Seamlessly Using Copilot.Live Streamlined Process
Hedefleri ve Hedef Kitleyi Tanımlayın
Start by clearly outlining the goals of your manufacturing chatbot, whether it's optimizing production workflows, managing inventory, or improving customer service. Identify your target audience, understanding their needs and pain points to tailor the bot's interactions effectively.
Şablonu Seçin Veya Özelleştirin
Select from Copilot.Live library of pre-built chatbot templates designed specifically for the manufacturing industry. Alternatively, customize your bot's design, conversation flows, and functionalities to align with your brand identity and unique requirements.
Araçları ve Sistemleri Entegre Edin
Seamlessly integrate your chatbot with tools and systems used in the manufacturing industry, such as enterprise resource planning (ERP) software, warehouse management systems (WMS), or supply chain management platforms. Ensure smooth data flow and automation across your organization's workflows.
Dağıtın ve İzleyin
Once configured, deploy your manufacturing chatbot across your website, intranet, or internal communication channels. Monitor its performance using analytics tools provided by Copilot.Live, analyzing user interactions, identifying areas for improvement, and optimizing the bot over time to enhance operational efficiency and customer satisfaction.
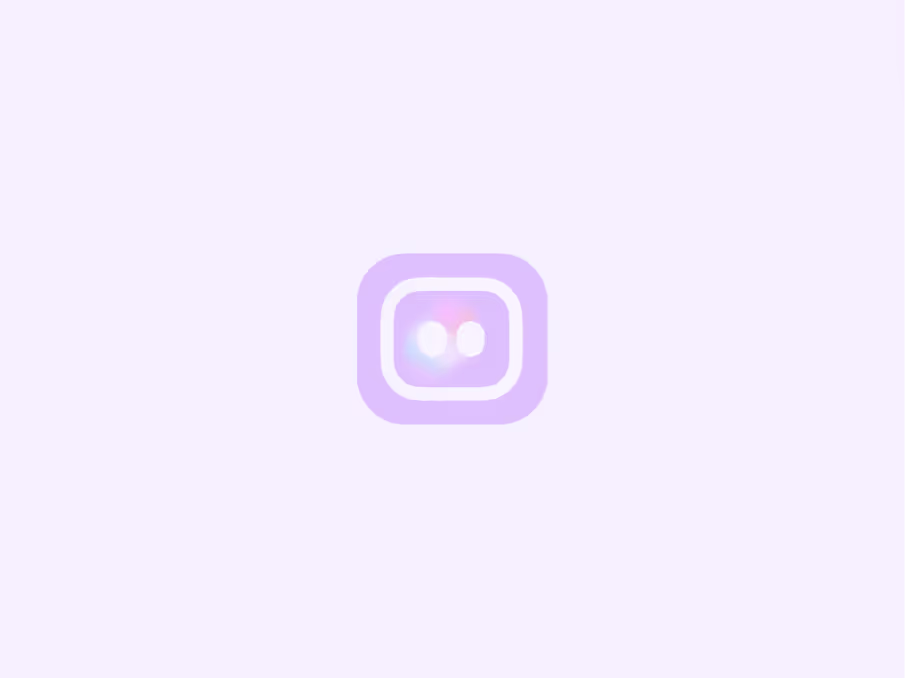
Chatbot Solutions For The Manufacturing Industry
Dive into the future of manufacturing efficiency with our cutting-edge chatbot solutions tailored specifically for the industry's evolving needs. In today's competitive landscape, optimizing processes and enhancing productivity are paramount for manufacturing businesses. Our chatbots offer seamless integration, intuitive user experiences, and advanced AI capabilities to streamline production workflows, manage inventory effectively, and improve customer service.
-
With features like natural language understanding, 24/7 availability, and integration with existing systems, our solutions empower manufacturing businesses to stay ahead of the curve. Explore how our chatbot solutions can revolutionize manufacturing operations, drive efficiency, and boost your bottom line. Let's embark on a journey to redefine manufacturing excellence together.
Why Choose Copilot.Live For Your Manufacturing Chatbot Needs?
Anında Yardım
Our chatbots offer 24/7 support, providing instant assistance to employees with any inquiries or issues they may encounter on the production floor. Whether accessing information about inventory levels or troubleshooting equipment problems, employees can rely on our chatbots for quick and efficient resolution, ensuring smooth operations round the clock.
Envanter yönetimi
Our chatbots seamlessly integrate with inventory management systems, allowing employees to check stock levels, place orders, and track shipments directly through the chat interface. By automating these processes, our chatbots streamline inventory management and reduce the risk of stockouts or overstocking, improving operational efficiency and cost-effectiveness.
Production Scheduling
Our chatbots assist production managers in creating and managing production schedules, optimizing resource allocation and minimizing downtime. By analyzing machine availability, workforce capacity, and order priorities, our chatbots generate optimized production schedules that maximize efficiency and meet customer demand. Additionally, employees can receive real-time updates and alerts about schedule changes or production delays, enabling proactive problem-solving and minimizing disruptions.
Quality Control
Our chatbots facilitate quality control processes by providing employees access to quality assurance protocols, inspection checklists, and troubleshooting guides. Employees can use the chat interface to report defects, document inspection results, and escalate issues to relevant personnel for resolution. By centralizing quality control procedures within the chatbot platform, manufacturing businesses can ensure consistent product quality, comply with industry regulations, and uphold customer satisfaction.
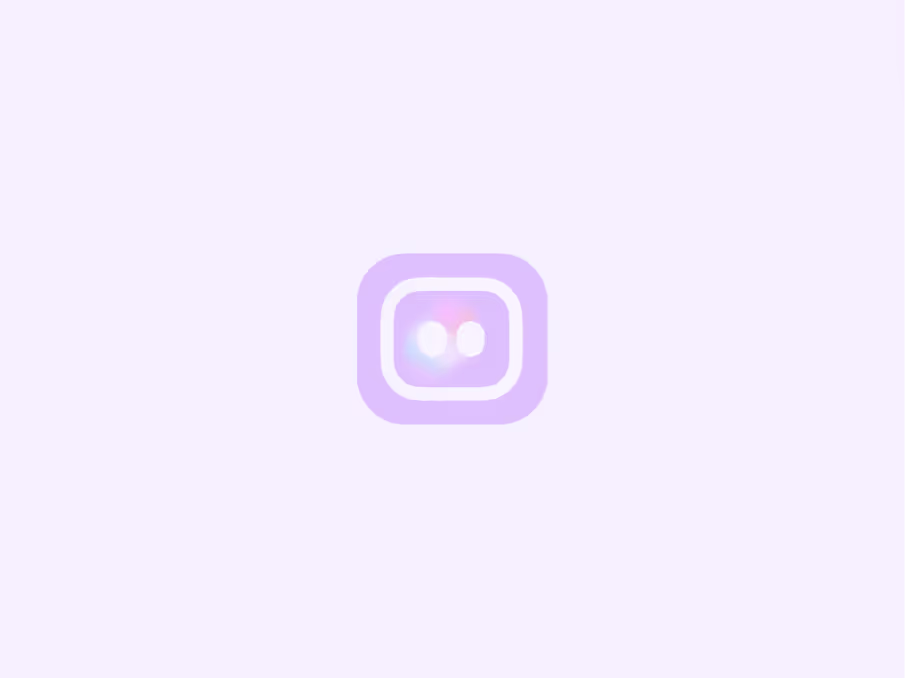
Revolutionizing Manufacturing With Copilot.Live
Maximizing productivity and efficiency while maintaining quality standards is essential in today's competitive manufacturing landscape. Copilot.Live leads the charge in revolutionizing the industry through advanced AI chatbots explicitly tailored for manufacturing businesses. Our cutting-edge technology seamlessly integrates into your operations, empowering your team to optimize production workflows, manage inventory effectively, and enhance customer service.
-
From production scheduling to supply chain management, our AI chatbots handle various tasks precisely and efficiently, ensuring seamless operations around the clock with Copilot.Live, you can stay ahead of the competition, improve operational efficiency, and drive growth in your manufacturing business. Join us in shaping the future of manufacturing with AI-driven innovation.
Key Features & Benefits Of Copilot.Live Chatbot For Manufacturing
Unlock unparalleled efficiency and productivity with Copilot.Live advanced chatbot for manufacturing. Discover how our innovative solution revolutionizes production workflows, inventory management, and customer service in the manufacturing industry.
Otomatik Geri Bildirim Toplama
Automated Feedback Collection streamlines the gathering of feedback from employees, customers, and other stakeholders. By automating feedback collection processes, businesses can gather performance insights, identify improvement areas, and drive continuous innovation.
Etkinlik Planlama Yardımı
Event Scheduling Assistance facilitates the planning and coordinating events such as production meetings, training sessions, and conferences. Our chatbots streamline event management processes and improve communication by providing employees with access to event information and scheduling tools.
Envanter yönetimi
Inventory Management functionality allows employees to check stock levels, place orders, and track shipments directly through the chat interface. By automating inventory management processes, our chatbots help businesses optimize inventory levels, reduce carrying costs, and improve supply chain efficiency.
Quality Control
Quality Control functionality provides employees access to quality assurance protocols, inspection checklists, and troubleshooting guides. By facilitating quality control processes, our chatbots help businesses ensure consistent product quality and compliance with industry standards.
Launch Your AI-Powered Chatbot In No Time
Kestirimci Bakım Uyarıları
Predictive Maintenance Alerts involve using data analytics and machine learning algorithms to predict when manufacturing equipment will likely fail or experience issues. The system can identify patterns and indicators that precede failures by analyzing historical data on equipment performance, such as sensor readings, operating conditions, and maintenance records. When certain conditions or patterns are detected, the system generates alerts or notifications to maintenance teams, prompting them to take preventive action before a breakdown occurs. This proactive approach helps minimize unplanned downtime, reduce maintenance costs, and extend the lifespan of critical assets.
Supply Chain Optimization Suggestions
Supply Chain Optimization Suggestions refer to recommendations provided by the chatbot to enhance efficiency, reduce costs, and improve performance across the supply chain. These suggestions are based on data analysis of various factors such as demand forecasts, inventory levels, supplier performance, and transportation logistics. The chatbot may propose optimizing inventory levels, consolidating orders, identifying alternative suppliers, or streamlining transportation routes. By implementing these optimization suggestions, manufacturing businesses can minimize lead times, reduce inventory holding costs, enhance customer service levels, and improve overall supply chain performance.
Regulatory Compliance Updates
Regulatory Compliance Updates entail real-time notifications and information the chatbot provides regarding changes, updates, or new regulations relevant to the manufacturing industry. These updates may include changes in environmental regulations, safety standards, labour laws, or industry-specific compliance requirements. By keeping users informed about regulatory changes, the chatbot helps manufacturing businesses stay compliant with legal obligations and industry standards. This proactive approach ensures businesses can adapt their processes, procedures, and policies accordingly, avoiding potential fines, penalties, or reputational damage associated with non-compliance.
Customized Production Reports
Customized Production Reports are tailored reports generated by the chatbot to provide detailed insights into manufacturing operations. These reports are customized based on specific user requirements, such as production metrics, quality performance, downtime analysis, or resource utilization. Users can specify the parameters, metrics, and timeframes they want to analyze, and the chatbot generates reports accordingly. These reports help manufacturing businesses track key performance indicators (KPIs), identify trends, pinpoint areas for improvement, and make data-driven decisions to optimize production processes. By providing relevant and actionable information, customized production reports enable businesses to enhance efficiency, reduce costs, and improve overall performance.
Environmental Impact Monitoring
Environmental Impact Monitoring involves the chatbot tracking and analyzing various environmental factors and their effects on manufacturing operations. This may include monitoring energy consumption, waste generation, emissions, and other environmental metrics. The chatbot collects data from sensors, meters, and other monitoring devices deployed throughout the manufacturing facility. It then uses this data to assess the production processes' environmental impact and identify improvement opportunities. The chatbot monitors environmental metrics in real-time and helps manufacturing businesses identify inefficiencies, implement sustainability initiatives, and comply with environmental regulations. This proactive approach enables businesses to reduce their environmental footprint, minimize resource usage, and promote sustainable practices.
Employee Performance Feedback
Employee Performance Feedback refers to the process facilitated by the chatbot for providing assessments and evaluations of employees' work performance. Through the chatbot interface, supervisors and managers can offer feedback on various aspects of an employee's performance, including strengths, areas for improvement, and accomplishments. This feedback can be provided in real time or during regular performance reviews. The chatbot may facilitate two-way communication, allowing employees to respond to feedback, ask questions, or seek clarification. By enabling timely and constructive feedback, the chatbot helps employees understand expectations, identify areas for growth, and improve their performance, ultimately contributing to the organisation's overall success.
Material Traceability Information
Material Traceability Information involves the chatbot providing detailed data and insights about materials' origin, movement, and usage throughout the manufacturing process. This includes information about the source of raw materials, suppliers, production locations, and distribution channels. The chatbot tracks materials from procurement to final assembly or shipment, ensuring transparency and accountability in the supply chain. It may also provide traceability information related to product batches or lots, enabling quick identification and resolution of quality issues or recalls. By offering comprehensive material traceability information, the chatbot helps manufacturing businesses ensure product quality, compliance with regulations, and customer satisfaction. This transparency also supports sustainability initiatives and ethical sourcing practices.
Augmented Reality (AR) Assistance
Augmented Reality (AR) Assistance integrates augmented reality technology into the chatbot interface to provide on-demand visual guidance and support for manufacturing tasks. Through AR overlays on mobile devices or wearable devices like smart glasses, users can access interactive visual instructions, diagrams, or animations overlaid in the real-world environment. This technology enables users to receive step-by-step instructions for equipment setup, maintenance procedures, troubleshooting, or assembly processes. AR-enhanced chatbots improve efficiency, accuracy, and safety in manufacturing operations by providing immersive and hands-free assistance. Users can quickly access relevant information, visualize complex procedures, and perform tasks more effectively, ultimately enhancing productivity and reducing errors.
Workflow Automation Recommendations
Workflow Automation Recommendations involve the chatbot suggesting opportunities for automating manual tasks and processes within the manufacturing workflow. The chatbot identifies areas where automation can improve efficiency, reduce errors, and free up human resources for more value-added tasks by analysing data on repetitive or time-consuming activities. These recommendations may include suggestions for implementing robotic process automation (RPA), workflow orchestration tools, or software automation solutions tailored to specific manufacturing processes. By streamlining workflows and reducing reliance on manual intervention, automation recommendations provided by the chatbot help manufacturing businesses optimize productivity, minimize costs, and accelerate time-to-market for products.
Quality Assurance Checklists
Quality Assurance Checklists provided by the chatbot offer comprehensive lists of criteria and tasks that ensure products meet specified quality standards throughout manufacturing. These checklists cover various aspects of production, including material inspection, assembly procedures, testing protocols, and packaging requirements. By following these checklists, manufacturing teams can systematically verify that each process step meets quality requirements and regulatory compliance. The chatbot may also facilitate the documentation of inspection results, deviations, and corrective actions, ensuring transparency and accountability in quality assurance practices. By promoting consistency and thoroughness in quality control efforts, these checklists help manufacturing businesses maintain high product quality, minimize defects, and enhance customer satisfaction.
Continuous Improvement Suggestions
Continuous Improvement Suggestions the chatbot provides involve recommendations for ongoing enhancements and optimizations to manufacturing processes, systems, and workflows. These suggestions are based on data analysis, industry best practices, and stakeholder feedback. The chatbot identifies areas with potential for improvement, such as reducing waste, increasing efficiency, or enhancing product quality, and proposes actionable suggestions for implementing changes. These suggestions may include process refinements, technology upgrades, training initiatives, or organizational adjustments to drive continuous improvement. By fostering a culture of innovation and learning, continuous improvement suggestions help manufacturing businesses stay competitive, adapt to changing market conditions and achieve operational excellence over time.
Cross-Departmental Communication
Cross-departmental communication facilitated by the chatbot enables seamless communication and collaboration among different departments within the manufacturing organization. The chatbot is a centralized platform where employees from various departments can exchange information, share updates, and collaborate on projects in real-time. It may provide features such as group messaging, file sharing, task assignments, and project tracking to facilitate effective team communication and coordination. By breaking down silos and promoting transparency, cross-departmental communication supported by the chatbot enhances collaboration, accelerates decision-making, and improves overall organizational agility. This streamlined communication ensures that all departments are aligned towards common goals, increasing efficiency and productivity across the manufacturing enterprise.
Root Cause Analysis Assistance
Root Cause Analysis Assistance involves the chatbot providing support and guidance to manufacturing teams in identifying the underlying causes of issues or problems encountered during production processes. The chatbot guides users through structured problem-solving methodologies, such as the "5 Whys" technique or fishbone diagrams, to systematically analyze symptoms, identify contributing factors, and uncover root causes. It prompts users to ask probing questions, gather relevant data, and consider various hypotheses to pinpoint the root cause of the issue. Additionally, the chatbot may provide access to historical data, documentation, or expert knowledge to aid in the analysis process. By facilitating root cause analysis, the chatbot helps manufacturing teams address issues at their source, implement practical corrective actions, and prevent the recurrence of problems, improving overall process reliability and product quality.
Energy Efficiency Recommendations
Energy Efficiency Recommendations provided by the chatbot offer tailored suggestions for reducing energy consumption and optimizing energy usage within manufacturing operations. These recommendations are based on analysing energy usage patterns, equipment efficiency, and process optimization opportunities. The chatbot may suggest upgrading to energy-efficient equipment, implementing automated controls, optimizing production schedules to reduce energy peaks, or investing in renewable energy sources. By implementing these recommendations, manufacturing businesses can lower energy costs, minimize environmental impact, and enhance sustainability efforts. Additionally, improved energy efficiency can contribute to regulatory compliance, reduce greenhouse gas emissions, and strengthen the organization's reputation as a responsible corporate citizen.
Supplier Performance Tracking
Supplier Performance Tracking involves the chatbot monitoring and evaluating the performance of suppliers based on various key performance indicators (KPIs) and metrics. These metrics may include delivery reliability, product quality, responsiveness to inquiries, adherence to specifications, and overall customer satisfaction. The chatbot collects data on supplier performance from various sources, such as purchase orders, delivery schedules, quality control reports, and feedback from internal stakeholders. It then analyzes this data to assess supplier performance against predefined benchmarks or service level agreements (SLAs). By tracking supplier performance, the chatbot helps manufacturing businesses identify top-performing suppliers, mitigate risks associated with poor performance, and drive continuous improvement in the supply chain. This proactive approach enables businesses to make informed decisions about supplier selection, contract negotiations, and relationship management, ultimately enhancing overall supply chain efficiency and effectiveness.
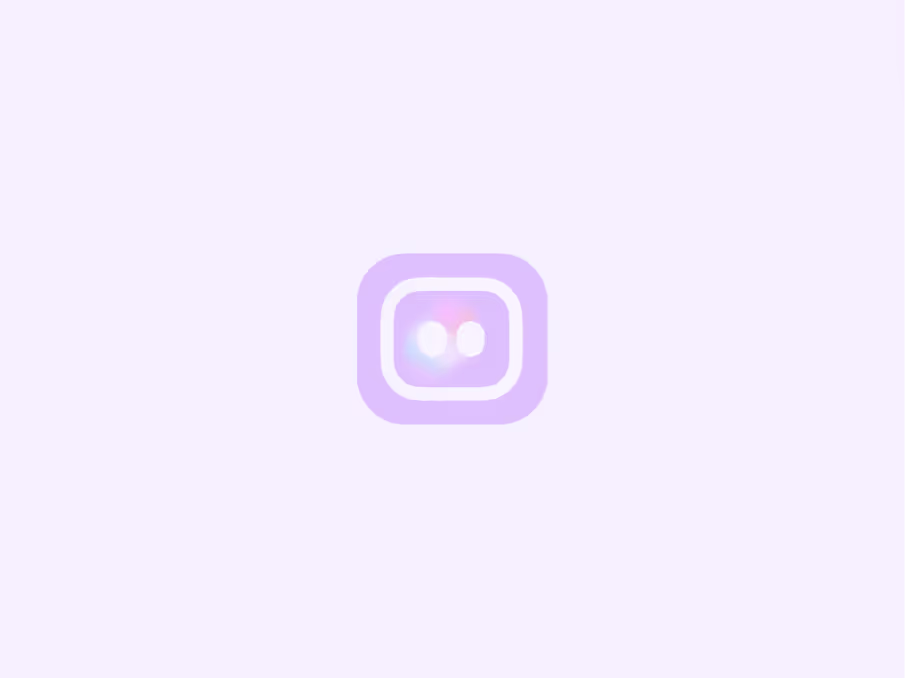
Transform Your Operations With AI-Driven Solutions
Embark on a journey towards manufacturing excellence with our AI-driven solutions tailored to revolutionize your operations. In today's fast-paced industrial landscape, achieving and surpassing operational benchmarks is paramount for sustained success. Our cutting-edge AI solutions are designed to empower manufacturing businesses, driving efficiency, quality, and innovation to unprecedented levels. From predictive maintenance alerts to energy efficiency recommendations, our chatbot seamlessly integrates into your processes, offering real-time insights, actionable suggestions, and automated assistance across all facets of your operations.
-
Whether optimizing workflows, refining quality control, or strengthening supplier relationships, our AI solutions are crafted to address your unique needs and deliver measurable outcomes. Join us as we redefine the future of manufacturing excellence through AI-driven innovation. Let's chart a course together towards unparalleled performance and lasting success.
What Does A Manufacturing Chatbot Need To Know?
Operational efficiency. To fulfil its role effectively, the chatbot must comprehensively understand various aspects of manufacturing operations. This includes detailed knowledge of equipment specifications, maintenance procedures, and troubleshooting protocols to provide timely assistance and resolve issues efficiently. Additionally, the chatbot should be well-versed in production workflows, encompassing scheduling, inventory management, and quality control processes, allowing it to offer insights and recommendations for process optimization and resource allocation.
-
Moreover, the chatbot needs to be equipped with information regarding safety regulations, compliance standards, and industry best practices to uphold a safe and compliant working environment. This knowledge enables the chatbot to guide users in adhering to regulatory requirements and implementing best practices for risk mitigation. Furthermore, integration with other systems and databases is essential for the chatbot to access real-time data on production metrics, supply chain status, and customer orders.
-
This integration facilitates seamless communication and decision-making across the organization, empowering users with timely and relevant information to drive operational excellence and meet business objectives. In essence, a manufacturing chatbot's effectiveness hinges on its ability to possess diverse knowledge spanning equipment, workflows, regulations, and data integration. By leveraging this knowledge, the chatbot becomes a valuable asset in streamlining operations, enhancing productivity, and driving continuous improvement within the manufacturing environment.
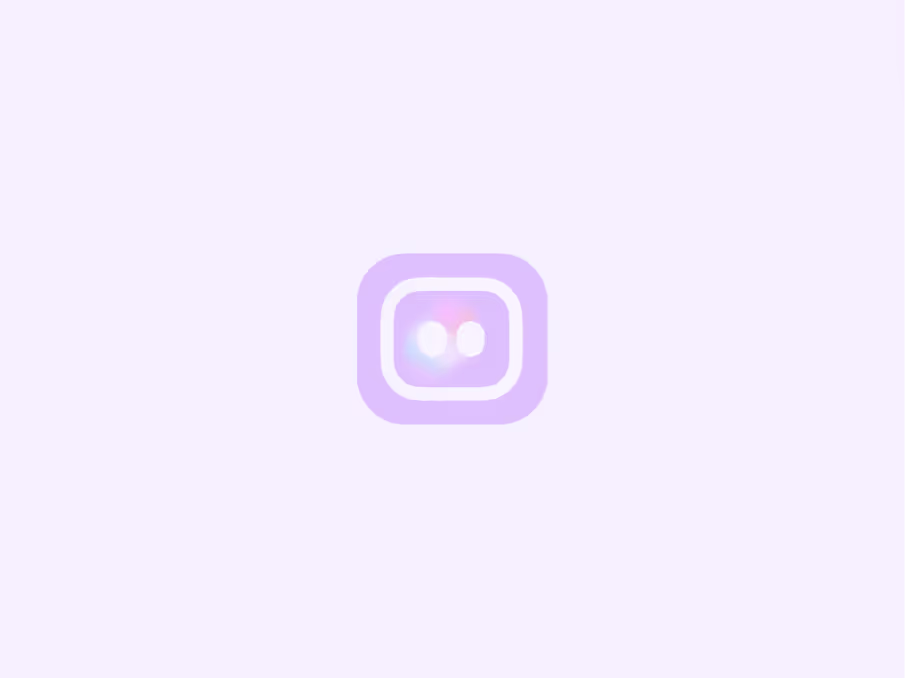
Sıkça Sorulan Sorular
Herhangi bir sorunuz, geri bildiriminiz veya öneriniz olması durumunda[email protected] bize ulaşabilir veya aşağıyı okuyabilirsiniz.
A. The manufacturing chatbot provides various services, including equipment troubleshooting, production scheduling assistance, quality control support, and supply chain management insights.
A. You can interact with the chatbot through text input on your computer, smartphone, or any device with internet access. Simply type your questions or commands, and the chatbot will respond promptly.
A. Yes, the chatbot is available round-the-clock to assist you with your inquiries and provide support whenever you need it, day or night.
A. Absolutely The chatbot is equipped with detailed knowledge of equipment specifications and troubleshooting procedures to assist you in diagnosing and resolving issues efficiently.
A. The chatbot's responses are highly accurate, thanks to its advanced natural language processing capabilities and access to up-to-date information about manufacturing processes and best practices.
A. Yes, the chatbot integrates with production systems and databases to provide real-time insights into production metrics, inventory levels, and order statuses.
A. Certainly The chatbot can help you with production scheduling by recommending optimizing production workflows, allocating resources effectively, and managing production timelines.
C. Chatbot, bilgilerinizin gizliliğini sağlamak için katı güvenlik protokollerini takip eder. Veri aktarımını şifreler ve gizliliğinizi korumak için gizlilik düzenlemelerine uyar.
A. Yes, the chatbot allows you to submit feedback, report any issues or concerns, and request assistance with any aspect of your manufacturing processes. Your feedback improves the chatbot's performance and enhances your experience.
A. The chatbot is a complimentary service to enhance manufacturing operations. There are no additional charges for using the chatbot's services.
Basitleştirin ve Dönüştürün
Bugünkü Müşteri Desteğiniz
Web sitenizi GPT destekli özel bir sohbet robotuyla yükseltin. Web sitenizde daha iyi bir kullanıcı deneyimi ve etkileşim için Copilot'unuzu bugün oluşturun.